Setting up a steel ingot from scrap business in India can be highly profitable because of the country’s high steel demand and ample scrap supply. In this guide, we will explore why and how to set up a steel ingot from scrap business in India, explaining the benefits of this venture and providing a step-by-step process to start your business, including the production of starting steel ingot. You’ll learn about raw materials, manufacturing processes, necessary machinery, investment costs, and market opportunities.
Key Takeaways
- The steel ingot from scrap business in India supports both economic growth and environmental sustainability by recycling metal and creating job opportunities.
- Starting a steel ingot business requires a careful selection of raw materials and specialized machinery, along with a detailed project report to ensure market viability and compliance.
- The Indian steel ingot market is projected to experience significant growth, driven by demand in construction and automotive sectors, presenting substantial opportunities for new ventures.
Overview of the Steel Ingot from Scrap Business
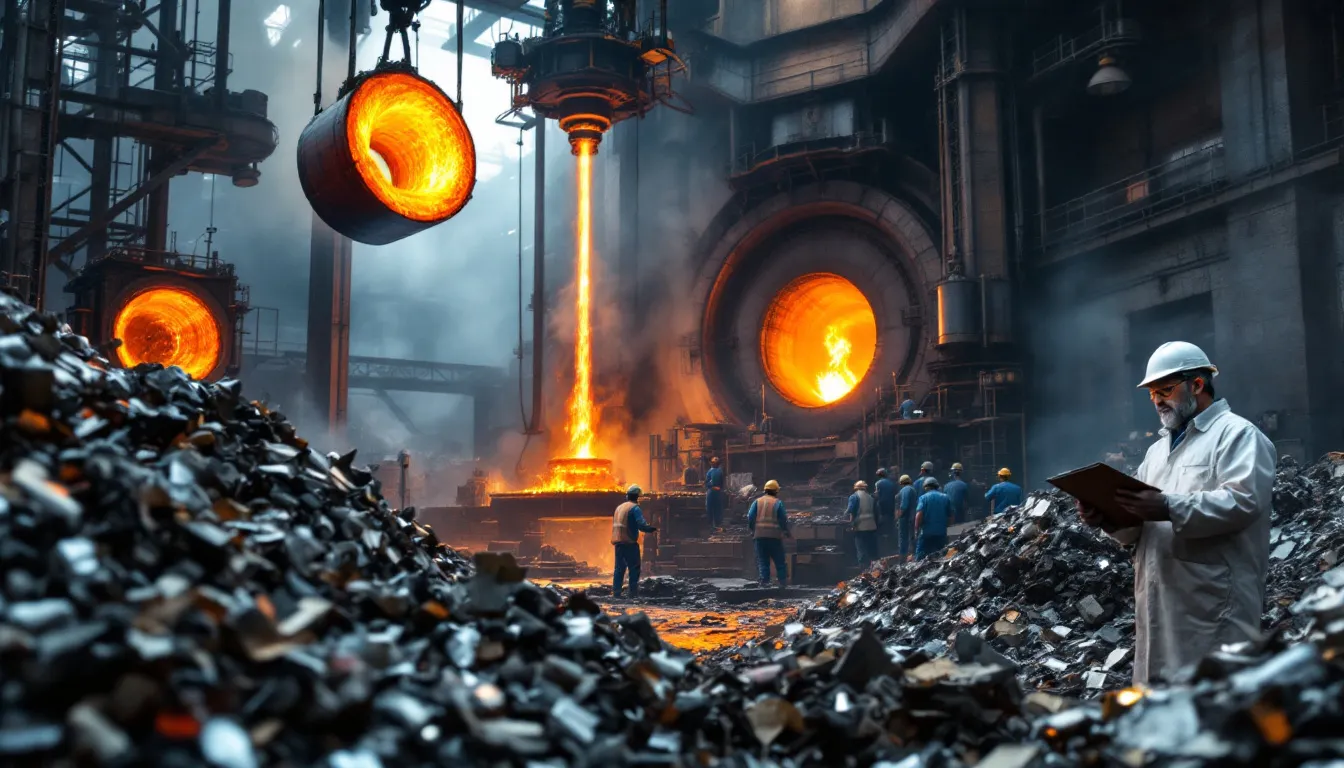
India stands as a dominant player in the global steel industry, ranking as the second-largest producer of crude steel. This impressive stature is bolstered by the country’s extensive production capabilities, which include a significant focus on the steel ingot from scrap sector. Steel production in India primarily relies on iron ore, coal, and scrap steel, making the recycling of scrap metal an integral part of the industry.
The steel ingot from scrap business involves converting discarded metal into valuable steel products. This process not only supports the steel industry but also contributes to environmental sustainability by reducing waste and conserving natural resources. Understanding the dynamics of this business allows entrepreneurs to tap into a lucrative market while promoting eco-friendly practices. The process begins with starting steel ingot production by heating and melting scrap materials to create molten steel, which is then poured into molds to form ingots.
Benefits of Starting a Steel Ingot from Scrap Business
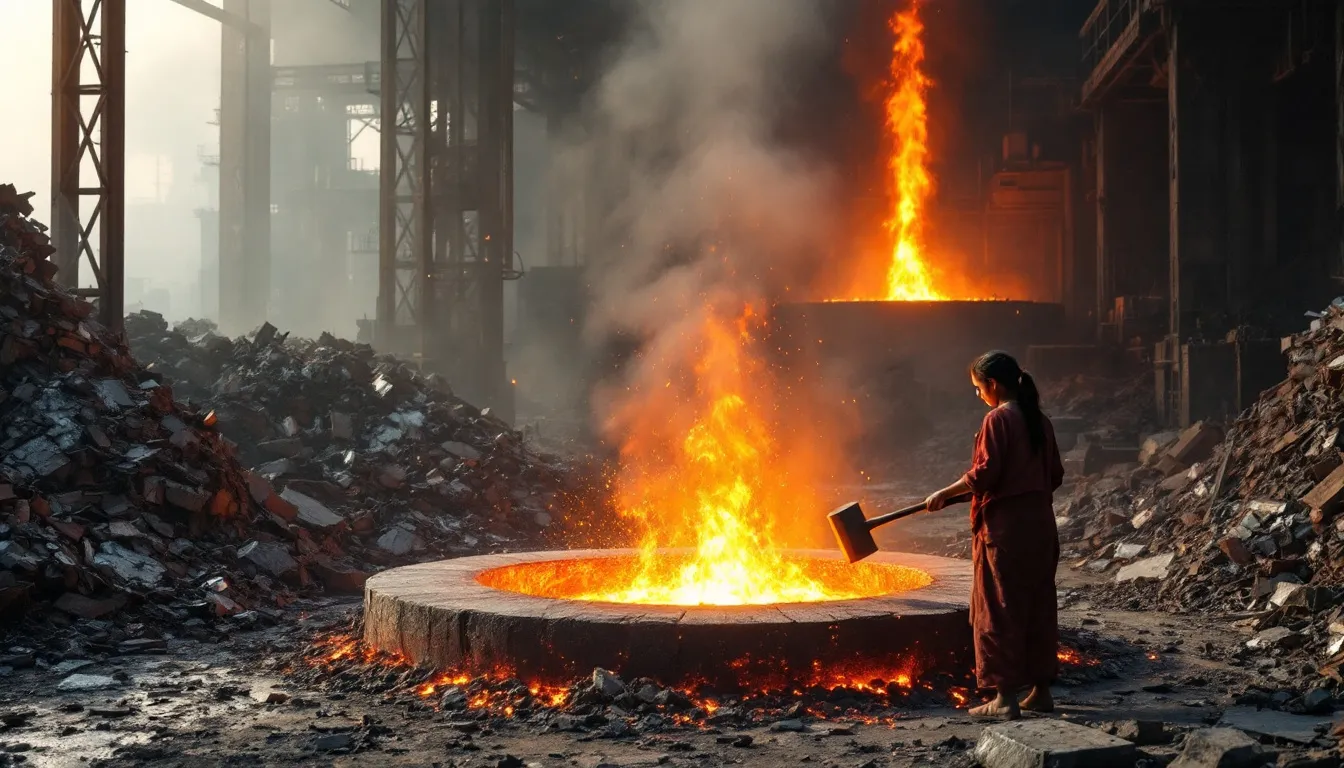
Starting a steel ingot from scrap business offers numerous benefits that extend beyond financial gains. The steel industry is a cornerstone of industrialization and economic growth in India, making it a vital sector for national development. By entering this market, entrepreneurs can create job opportunities within local communities, thereby supporting economic development and fostering industrial advancement.
Moreover, the profitability of this venture is driven by the increasing demand for recycled steel across various industries. The ability to recycle and repurpose scrap metal not only conserves natural resources but also significantly reduces energy consumption. Recycling aluminum, for instance, saves up to 95% of the energy required to produce it from raw materials. This energy efficiency translates into cost savings and a smaller carbon footprint, aligning with global sustainability goals.
Recycling metals also plays a crucial role in minimizing waste accumulation in landfills, thereby addressing environmental concerns. This practice reduces greenhouse gas emissions, crucial in combating climate change. Thus, by starting a steel ingot from scrap business, entrepreneurs can contribute to both economic growth and environmental sustainability. Additionally, the economic benefits and market demand for starting steel ingot production further enhance the viability of this business.
Understanding the Raw Materials Required
Producing steel ingots from scrap requires a careful selection of raw materials to ensure high-quality output. The primary raw material is scrap steel, which can be added to molten iron to enhance the composition of the final product. During the steelmaking process, recycled steel scrap contributes essential carbon, transforming pig iron into steel.
In addition to scrap steel, flux materials such as limestone are used to remove impurities from the metal mixture. Effective sorting of scrap metal is vital to segregate various metal types and eliminate contaminants, ensuring the production of high-quality steel. This process is crucial for creating the starting steel ingot.
A comprehensive project report should include an analysis of raw material availability, as India’s steel sector benefits from easy access to iron ore and competitive labor costs.
The Manufacturing Process of Steel Ingots from Scrap
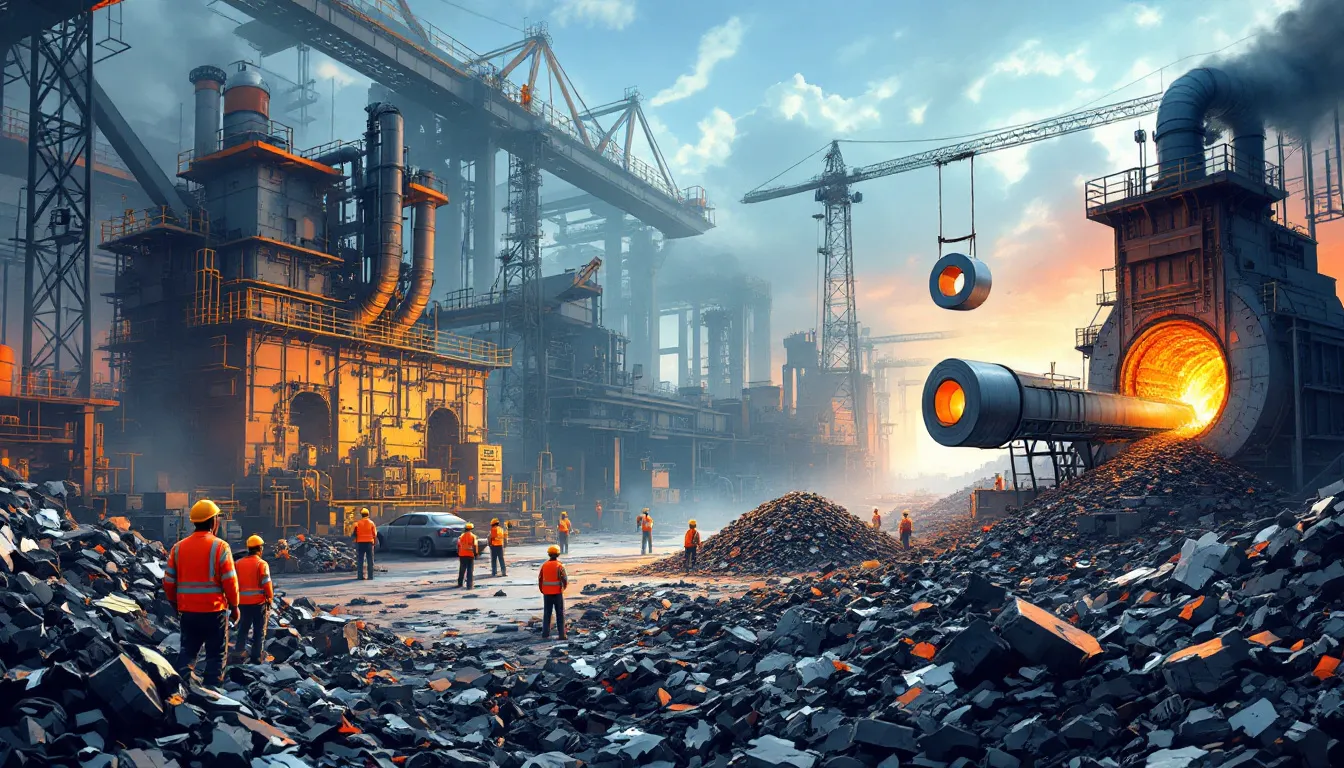
The manufacturing process of steel ingots from scrap involves several critical steps: collection and sorting of scrap metal, melting and refining, and finally, casting the molten steel into ingots. Each step is designed to ensure the highest quality of the final product while maximizing efficiency and minimizing waste. The process begins with the starting steel ingot, which is created by heating and melting scrap materials to form molten steel that is then poured into molds.
Collection and Sorting of Scrap Metal
The process begins with the collection and sorting of various types of scrap metal. This initial step ensures the quality of the material used in production. Scrap metal is categorized into bins for sorting, effectively identifying non-ferrous metals containing steel or iron.
This careful segregation is essential for maintaining the integrity of the final steel ingots.
Melting and Refining
In the melting phase, the collected scrap metal is heated in high-temperature furnaces, transforming it into liquid steel. This phase typically employs Electric Arc Furnaces (EAFs) or Induction Furnaces (IFs), which allow precise control over temperature and material composition. The molten steel is then refined to remove impurities and enhance its properties.
Refining is a critical part of the process as it ensures the removal of unwanted elements, resulting in high-quality molten steel. The refined liquid steel is now ready for the next stage: casting into steel ingots. This step ensures the final product meets industry standards and customer requirements.
Casting into Steel Ingots
The continuous casting process forms steel ingots from molten steel. During this process, the molten steel is carefully poured into designated molds, which shape the material into ingots. These molds are designed to withstand high temperatures and facilitate the easy release of the solidified ingots, ensuring uniformity and quality.
Adopting continuous casting techniques enhances production efficiency, reduces waste, and improves overall output rates. This method is widely used in the industry due to its ability to produce high-quality steel ingots consistently.
Formula for Steel Ingot Composition
The formula for producing steel ingots from scrap involves a precise balance of input materials, energy consumption, and desired output specifications. Key components include scrap steel, flux materials, and various additives to create steel ingots that achieve the required chemical composition.
Maintaining quality standards and adhering to guidelines ensures consistency in steel production. These standards ensure that the final product meets industry requirements and customer expectations. By following a well-defined formula, manufacturers can produce steel ingots that are both high-quality and cost-effective. The process begins with the starting steel ingot, which is produced by heating and melting scrap materials to create molten steel that is then poured into molds.
Machinery and Equipment Needed
The production of steel ingots from scrap requires specialized machinery and equipment. Electric Arc Furnaces (EAFs) are commonly used to melt scrap metal, enabling the charging of 100% scrap, though precise control of chemical composition can be challenging. Induction Furnaces (IFs) are also utilized, particularly in regions like India and China, due to their lower initial investment costs despite limited refining options.
In addition to melting furnaces, steel ingot casting requires specialized molds made from cast iron, which facilitate easier removal of the solidified ingots due to their thermal properties. Casting machines and various types of conveyors are also essential for the production process.
Additional machinery like cranes and material handling equipment is necessary to manage the heavy scrap material and finished products. These tools ensure smooth operations and enhance overall efficiency in the plant. Starting steel ingot production involves these critical components to ensure a streamlined and effective manufacturing process.
Investment and Costs
Starting a steel ingot from scrap business in India requires a significant investment. Capital requirements should be broken down to understand the necessary investment for machinery, raw materials, and operational costs. A break-even analysis determines when the business will start to generate profit. Additionally, understanding the process of producing a starting steel ingot from scrap metal is crucial for planning and cost estimation.
One of the key challenges in this sector is the availability and cost fluctuations of raw materials, which can adversely affect the manufacturing process. Entrepreneurs should be prepared to navigate these challenges and plan their investments accordingly to ensure sustainability and profitability.
Market Demand and Opportunities in India
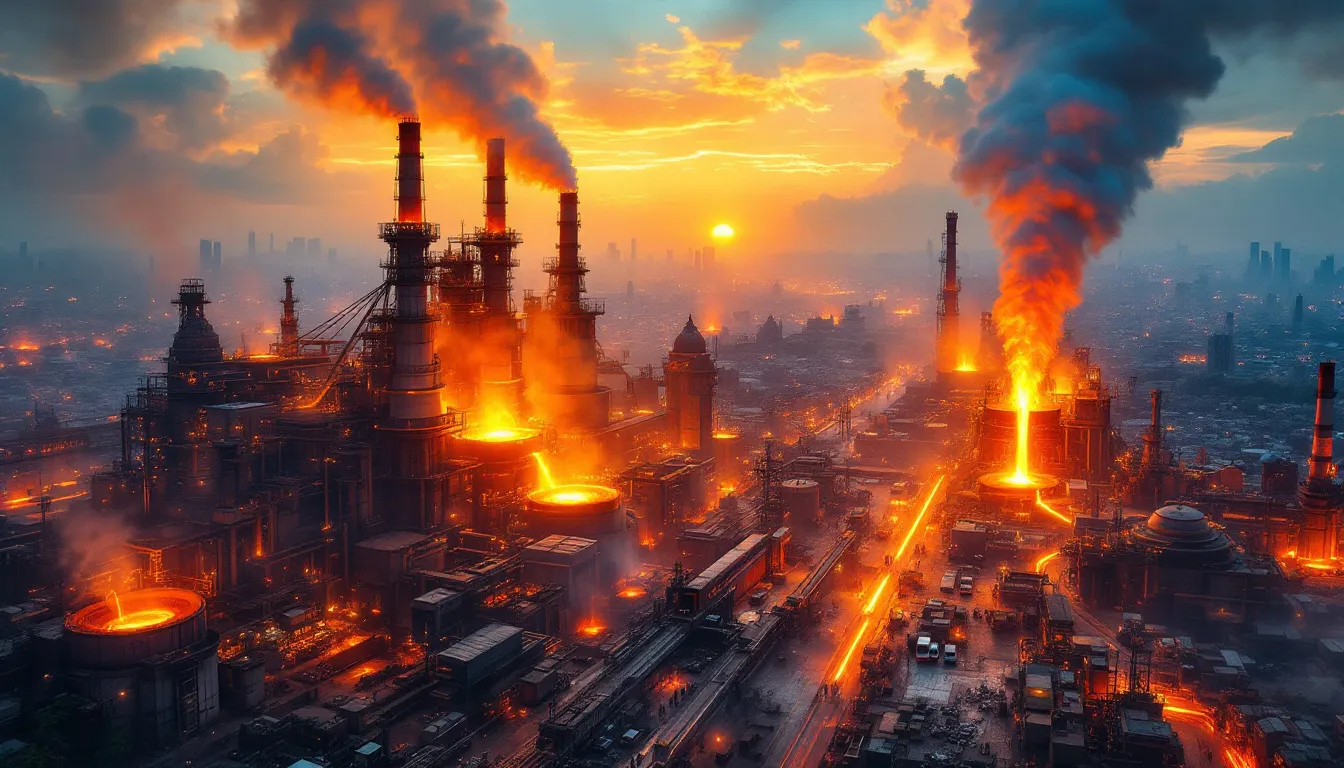
The Indian steel ingots market has experienced consistent growth, driven by rising demand from sectors like construction and automotive. The market for steel ingots in India was valued at approximately Rs 21 billion (~USD 300 million) in 2018, reflecting a CAGR of around 15% since 2015.
Demand for steel ingots is primarily driven by increasing needs in construction, automotive, and manufacturing sectors, especially in emerging economies. Government initiatives aimed at infrastructure development are significantly influencing the growth of the steel ingot market, particularly in regions with emerging economies.
The Indian steel industry, classified into primary, secondary, and large producers, is crucial for the economy, with India being the second-largest producer of crude steel since April 2022. Effective market research in the steel ingot sector includes analyzing demand trends from key industries such as construction and automotive.
Global Market Outlook for Steel Ingots from Scrap
The global market for steel ingots from scrap is robust, with significant trade in ferrous scrap originating from major exporting regions like the European Union and North America. In 2022, approximately 94.8% of total world steel trade figures were derived from 62 countries, highlighting the concentrated nature of the industry.
Major importers of steel, including products from scrap, are found in regions such as Asia and North America, signaling strong demand dynamics. These regions offer substantial business opportunities for entrepreneurs looking to engage in the global steel ingot market. The production of starting steel ingot plays a crucial role in meeting this global demand.
Revenue and Profit Projections
Revenue and profit projections are critical for assessing the viability of a steel ingot from scrap business. Detailed project plans typically include expected revenue and profit margins, providing a comprehensive financial overview. These projections help entrepreneurs understand the potential returns on their investment. Additionally, the process of producing a starting steel ingot from scrap metal can significantly impact these financial projections.
Operating expenses such as utilities, salaries, and maintenance costs are essential components of the overall financial plan. These costs need to be carefully managed to ensure profitability. A break-even analysis is also crucial for understanding the point at which income from sales equals total costs, helping to gauge the financial health of the business.
Quality control equipment is vital to ensure that the chemical composition and physical properties of the steel ingots meet industry standards. Profitability ratios, such as gross profit margin and net profit margin, are used to assess the financial efficiency of the steel ingot venture.
Steps to Set Up Your Steel Ingot from Scrap Business
Setting up a setup steel ingot from scrap business involves several critical steps, including legal compliance, market assessment, and financial forecasting. These steps are designed to ensure that the business is well-prepared to enter the market and achieve long-term success. Additionally, understanding the process of producing a starting steel ingot from scrap metal is crucial for efficient operations and meeting market demand.
Conducting Market Research
Conducting thorough market research is essential for identifying local demand and the availability of scrap metal resources. This research should analyze competitors to gain insights into successful business models and strategies.
Creating a Detailed Project Report
A comprehensive project report should cover various aspects such as market analysis, financial projections, and operational plans to guide the business setup. This report will highlight the potential for profit and sustainability in transforming scrap steel into ingots.
Financial projections in project reports help entrepreneurs understand capital requirements, including expenses for machinery and fixed assets. A detailed project report includes a breakdown of raw material costs and assessments of overheads, providing a complete financial overview.
Developing a Related Business Plan
Developing a related business plan is critical for articulating business goals and strategies. This plan should include revenue projections, market conditions, and initial investment requirements for setting up the steel ingot business.
The steel ingot from scrap business benefits from a growing market demand in India, driven by infrastructure development and increasing recycling needs. With proper planning, this business can yield significant profits and a good return on investment.
Importing and Exporting Steel Ingots from Scrap
Importing and exporting steel ingots from scrap can open up global market opportunities for businesses in India. Engaging in import and export statistics activities can increase profitability, provide access to new markets, and diversify supply chains. Starting steel ingot production from scrap metal can further enhance these opportunities by meeting market demand and promoting sustainable business practices.
The feasibility of engaging in these activities largely depends on regulatory compliance and market demand. By adhering to trade agreements and understanding market dynamics, businesses can enhance their sustainability and competitiveness in the global market.
PRB Consultancy Services
Project Report Bank (PRB Consultancy Services) is renowned for delivering a comprehensive range of technical consulting services aimed at empowering entrepreneurs with project feasibility assessments and market surveys. Established in 2016, PRB has emerged as a significant entity in the industrial consulting arena, catering to a diverse clientele both within India and internationally.
PRB adopts a methodical approach to consulting, ensuring that clients receive customized solutions based on thorough analysis and evaluation. The organization has developed over 10,000 project reports across various industries, showcasing its vast expertise and market insight.
Future Market Demand and Trends
The steel ingot market is projected to grow from USD 1.17 trillion in 2023 to USD 1.42 trillion by 2030, indicating a significant opportunity for new businesses. This growth reflects a compound annual growth rate (CAGR) of 4.2% from 2024 to 2030.
Understanding the demand for steel ingots is essential, as the market for steel scrap is expected to grow from 574.1 million metric tonnes in 2020 to 784.8 million metric tonnes by 2027. This increasing demand underscores the potential for entrepreneurs to capitalize on this market trend.
The COVID-19 pandemic initially disrupted the steel ingots market, but recovery was facilitated by government support and resumed economic activities. The steel ingot from scrap market is anticipated to have a compound annual growth rate of 4.6% between 2020 and 2027. The potential for starting steel ingot production is significant, given the economic benefits and market demand.
Environmental Impact and Sustainability
The steel ingot industry from scrap is significant in India due to its potential for recycling and sustainability. By utilizing scrap metal for ingot production, businesses can contribute to sustainable practices that reduce landfill waste and lower carbon footprints. The process of producing a starting steel ingot involves heating and melting scrap materials to create molten steel, which is then poured into molds to form ingots.
Steel is the most recycled material globally, with over 650 million tons recycled each year, saving significant amounts of iron ore, coal, and limestone compared to traditional steel production. This business model supports environmental sustainability by recycling steel, thus reducing waste in landfills.
Technological advancements, such as the rise of electric arc furnace (EAF) technology, are enhancing production efficiency and reducing environmental impact in the steel ingot market. These innovations make the steel ingot from scrap business a viable and eco-friendly venture.
Importance of a Detailed Project Report
A detailed project report is invaluable for answering critical business questions like feasibility, market research, cost, profitability, and risk assessment. This report covers financial projections, production estimates, and compliance requirements, providing a comprehensive guide for business setup. A detailed project report is crucial for starting steel ingot production.
Customized project reports are particularly valuable for investors and entrepreneurs, offering tailored insights that help in making informed decisions. By leveraging these reports, businesses can ensure a well-structured and strategic approach to entering the steel ingot from scrap industry.
Best Location for Setting Up a Steel Ingot from Scrap Plant in India
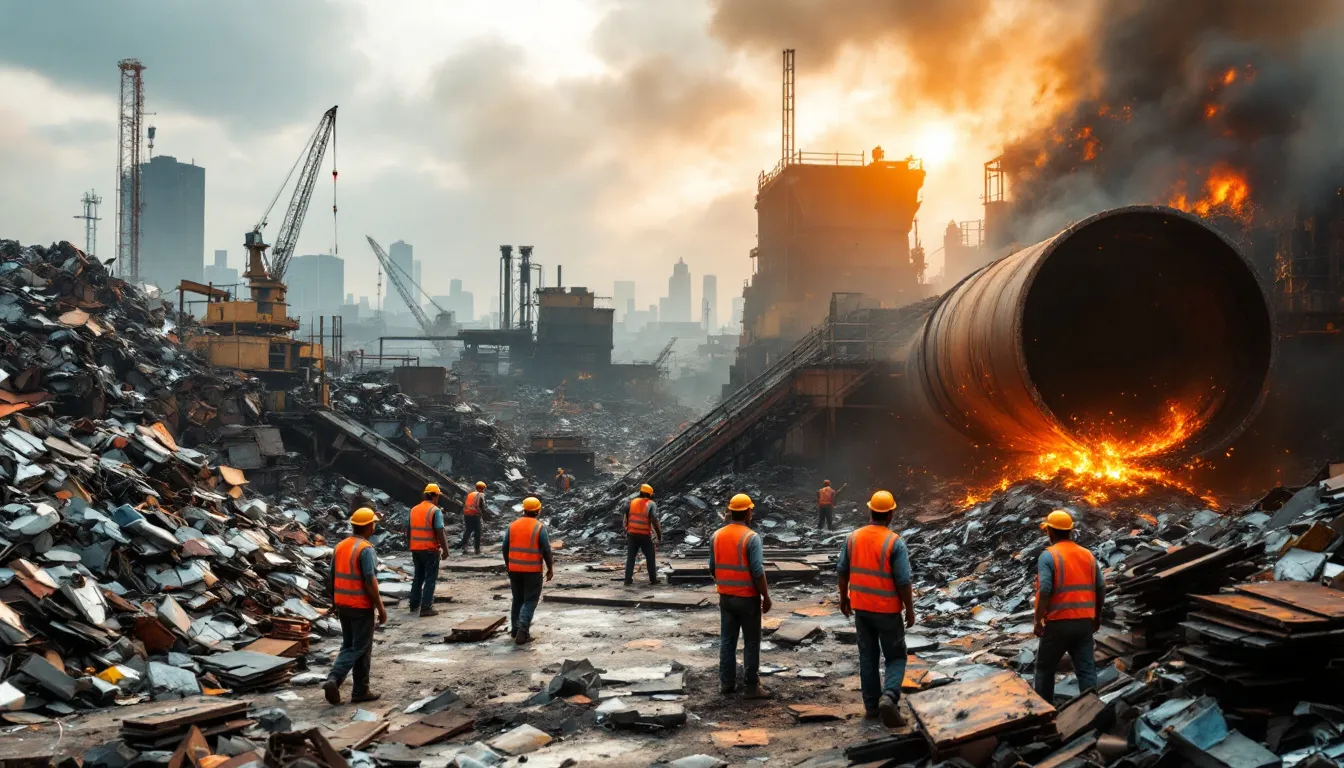
The location of a steel ingot plant plays a crucial role in determining the profitability and operational efficiency of the business. For steel recycling, proximity to raw materials, transport facilities, industrial infrastructure, and energy supply are key factors.
Recommended locations in India for setting up a steel ingot from scrap plant include regions with easy access to scrap metal resources and robust industrial infrastructure. These locations can significantly enhance operational efficiency and reduce logistical costs. Additionally, these regions are ideal for starting steel ingot production due to their strategic advantages.
Key Factors to Consider in Location Selection
- Proximity to Scrap Suppliers: Choosing a location near industries that generate scrap, such as automotive, construction, and shipbreaking, can significantly lower raw material expenses.
- Transportation and Infrastructure: Having access to efficient transport networks, including roads, railways, and ports, helps minimize logistics costs for both incoming raw materials and outgoing products.
- Energy Costs and Supply: Since steel recycling is energy-intensive, selecting regions with a stable and cost-effective power supply is crucial.
- Incentives and Subsidies: Some states provide tax incentives, electricity subsidies, and favorable policies for metal recycling, making it important to evaluate local government incentives.
- Proximity to Ports for Import and Export: Choosing a location near major ports can streamline logistics for importing raw materials and exporting steel ingots. This proximity reduces transportation costs and transit times, enhancing business efficiency and market reach.
- Locations with Favorable Energy Infrastructure: Establishing your plant in regions with reliable energy infrastructure is crucial, as energy costs are a significant part of steel ingot production. Access to cost-effective electricity ensures uninterrupted operations and boosts overall efficiency.
- Emerging Industrial Zones with Tax and Policy Benefits: Setting up in emerging industrial zones can offer tax incentives and supportive policies, reducing initial investment and operational costs. These zones often provide access to a network of suppliers and customers, fostering business growth.
Differences between manufacturing steel ingots from raw materials versus from scrap:
Aspect | Steel Ingot Manufacturing (from Raw Ore) | Steel Ingot Manufacturing (from Scrap) |
---|---|---|
Raw Material Source | Iron ore, mined and refined into steel | Recycled scrap metal from various industries |
Initial Processing | Involves mining, refining, and smelting iron ore | Directly melted after sorting and cleaning |
Production Complexity | Complex: includes mining, crushing, sintering, and coke-making | Streamlined: primarily melting, purifying, and casting |
Environmental Impact | Higher due to mining, energy-intensive processes, and carbon emissions | Lower environmental impact, reduces need for mining and lowers emissions |
Cost and Efficiency | More expensive due to additional stages and energy requirements | Generally cheaper, fewer stages and lower raw material costs |
Quality Control | Alloy composition can be precisely controlled for specific applications | Requires rigorous sorting and purification to maintain quality |
Applications | Ideal for high-grade steel requiring precise properties | Suitable for general industrial and construction applications |
Energy Requirements | High, especially for ore smelting and refining processes | Lower energy requirements, often uses electric arc or induction furnaces |
Sustainability | Less sustainable due to resource-intensive processes | More sustainable, conserves resources through recycling |
This table provides a quick overview of the key differences between the two methods, making it easier to understand their respective advantages and ideal applications. Additionally, the process of starting steel ingot production from scrap involves heating and melting scrap materials to create molten steel, which is then poured into molds to form ingots.
Layout of Plant
A well-designed steel ingot plant layout enhances efficiency by ensuring optimal flow of materials and minimizing handling time. The layout should segregate areas for melting, refining, casting, and finishing processes to maintain safety and operational efficiency. The initial steps of starting steel ingot production, including the heating and melting of scrap materials to create molten steel, should be carefully planned within the layout.
Incorporating adequate space for maintenance activities in the layout is crucial to facilitate uninterrupted operation and reduce downtime. Safety considerations, such as emergency exits and fire suppression systems, should be integral to the plant layout design.
Key Terms
To successfully establish a steel ingot from scrap business in India, one must delve into a comprehensive Detailed Project Report (DPR) that includes an Investment Analysis and an Economic Feasibility Study. This report should encompass an in-depth Market Research Report on the Steel Ingot from Scrap Industry, highlighting potential growth and profitability. Crafting a robust Steel Ingot from Scrap Business Plan is essential for navigating the complexities of the market. By understanding the economic feasibility of the project, entrepreneurs can make informed decisions and capitalize on emerging opportunities. Engaging with these related topics ensures a strategic approach to setting up a sustainable and profitable venture in the steel industry. Additionally, the process of producing a starting steel ingot from scrap metal involves heating and melting scrap materials to create molten steel, which is then poured into molds to form ingots.
Summary
In summary, the steel ingot from scrap business presents a promising opportunity for entrepreneurs in India. The industry not only supports economic growth and job creation but also contributes to environmental sustainability by recycling scrap metal. By understanding the raw materials, manufacturing processes, investment requirements, and market opportunities, entrepreneurs can establish a successful and profitable business. The process begins with producing a starting steel ingot from molten steel poured into molds.
The future of the steel ingot market looks bright, with significant growth projected in the coming years. By leveraging detailed project reports and strategic business plans, entrepreneurs can navigate the challenges and capitalize on the opportunities in this dynamic industry. Embrace the journey of transforming scrap into valuable steel ingots and contribute to a sustainable future.
Frequently Asked Questions
What are the primary raw materials required for producing steel ingots from scrap?
The primary raw materials required for producing steel ingots from scrap are scrap steel, flux materials like limestone, and various additives to ensure the desired chemical composition. The process begins with the starting steel ingot, where scrap materials are heated and melted to create molten steel, which is then poured into molds to form ingots.
What is the significance of a detailed project report in this business?
A detailed project report is significant as it offers essential insights into feasibility, market research, financial projections, and operational plans, enabling entrepreneurs to make well-informed decisions. Thus, it serves as a vital tool for successful business planning and execution. This is particularly crucial for starting steel ingot production.
How does the steel ingot from scrap business contribute to environmental sustainability?
The steel ingot from scrap business significantly enhances environmental sustainability by recycling metal, thereby reducing landfill waste, conserving natural resources, and lowering carbon emissions. This approach promotes a circular economy, minimizing the environmental impact of steel production. Additionally, the process of producing a starting steel ingot from scrap metal is crucial for various industrial applications and supports sustainable business practices.
What are the key factors to consider when choosing a location for a steel ingot plant in India?
When selecting a location for a steel ingot plant in India, it is essential to prioritize proximity to raw materials, efficient transport facilities, robust industrial infrastructure, and a reliable energy supply. These factors significantly influence operational efficiency and overall success. Additionally, the location should support the initial steps of starting steel ingot production.
What are the benefits of engaging in import and export activities for steel ingots?
Engaging in import and export activities for steel ingots enhances profitability, grants access to new markets, and diversifies supply chains, ultimately improving business sustainability and competitiveness in the global market. The process of producing a starting steel ingot from scrap metal involves heating and melting the scrap materials to create molten steel, which is then poured into molds to form ingots.
What is the Initial Investment Needed to Start a Steel Ingot Business?
The initial investment required to start a steel ingot business can vary significantly depending on several factors such as the scale of operations, location, and the type of machinery and technology used. On average, setting up a small to medium-sized steel ingot plant may require an investment ranging from INR 2 crore to INR 10 crore (approximately USD 250,000 to USD 1.25 million). This investment typically covers costs related to land acquisition, construction, machinery, raw materials, and working capital. It’s crucial for entrepreneurs to conduct a detailed project report and financial analysis to accurately estimate the total investment required for their specific business model. Additionally, understanding the process of producing a starting steel ingot from scrap metal is essential for planning and optimizing the initial investment.
Main Steps in the Manufacturing Process of Steel Ingots from Scrap
The process includes collecting and sorting scrap, melting it in an induction or electric arc furnace, removing impurities, adding alloys, and casting it into molds to form ingots.
This is the initial step in starting steel ingot production.
What kind of machinery is required to start this business?
Essential machinery includes a scrap crusher/shredder, an induction or electric arc furnace, a ladle, and ingot molds. Investing in quality machinery ensures efficient production. This machinery is crucial for starting steel ingot production, as it allows for the heating and melting of scrap materials to create molten steel, which is then poured into molds to form ingots.
Which are the best locations in India to set up a steel ingot plant?
Ideal locations include industrial areas in Maharashtra, Gujarat, Jharkhand, Odisha, Tamil Nadu, and Rajasthan due to their scrap availability, energy infrastructure, and transport links.
These regions are also ideal for starting steel ingot production.
What is the market demand for steel ingots in India?
Demand is high in sectors like construction, automotive, and infrastructure, with growing support from government initiatives to boost recycling and reduce reliance on imported steel.
The process of producing a starting steel ingot from scrap metal, which involves heating and melting scrap materials to create molten steel that is then poured into molds, is crucial for meeting this demand.
Is it possible to export steel ingots produced in India?
Yes, there is demand for high-quality steel ingots internationally. Strategic locations near ports (like Gujarat and Tamil Nadu) can facilitate easier export logistics.
How does a project report help in setting up a steel ingot business?
A project report provides comprehensive details on market research, financial projections, cost analysis, risk assessment, and compliance, helping entrepreneurs make informed decisions and secure funding. It is particularly crucial for starting steel ingot production.
Are there government subsidies or incentives for starting a steel ingot business?
Some states offer subsidies, tax benefits, or relaxed regulations for recycling businesses. It’s advisable to check with local authorities for any specific incentives in your state.
How long does it take to break even in the steel ingot manufacturing business?
The break-even period varies depending on factors like production capacity, operational costs, and market demand. Typically, a well-optimized operation can achieve profitability within 1-2 years.