Comprehensive Paver Block Project Report PDF: Setup Cost, Business Plan & Investment Opportunities
If you’re planning to venture into the paver block manufacturing business, you need detailed and reliable information. Our paver block project report PDF offers a thorough guide on setup costs, business plans, and potential profits, backed by market research worldwide. Dive in to discover real opportunities and actionable insights that can help you succeed.
Key Takeaways
- The paver block manufacturing business presents low entry barriers and high market demand driven by urbanization and infrastructure development.
- Setup costs involve land acquisition, machinery, raw materials, labor, and other operational expenses, with initial investments ranging from 20 Lakh to 50 Lakh.
- The global market for paver blocks is projected to grow significantly, indicating robust opportunities for investment, especially with the rising preference for sustainable construction materials.
Introduction
Small-scale manufacturing businesses have seen a significant rise in recent years, driven by the demand for quality building materials and the increasing focus on infrastructure development. Paver blocks, in particular, have gained popularity due to their durability, aesthetic appeal, and ease of installation.
With urbanization on the rise and the government’s push for infrastructure projects, the demand for paver blocks is expected to grow exponentially. This blog post aims to provide a comprehensive market overview, covering everything from setup costs and business plans to investment opportunities and detailed project reports.
What are Paver Blocks?
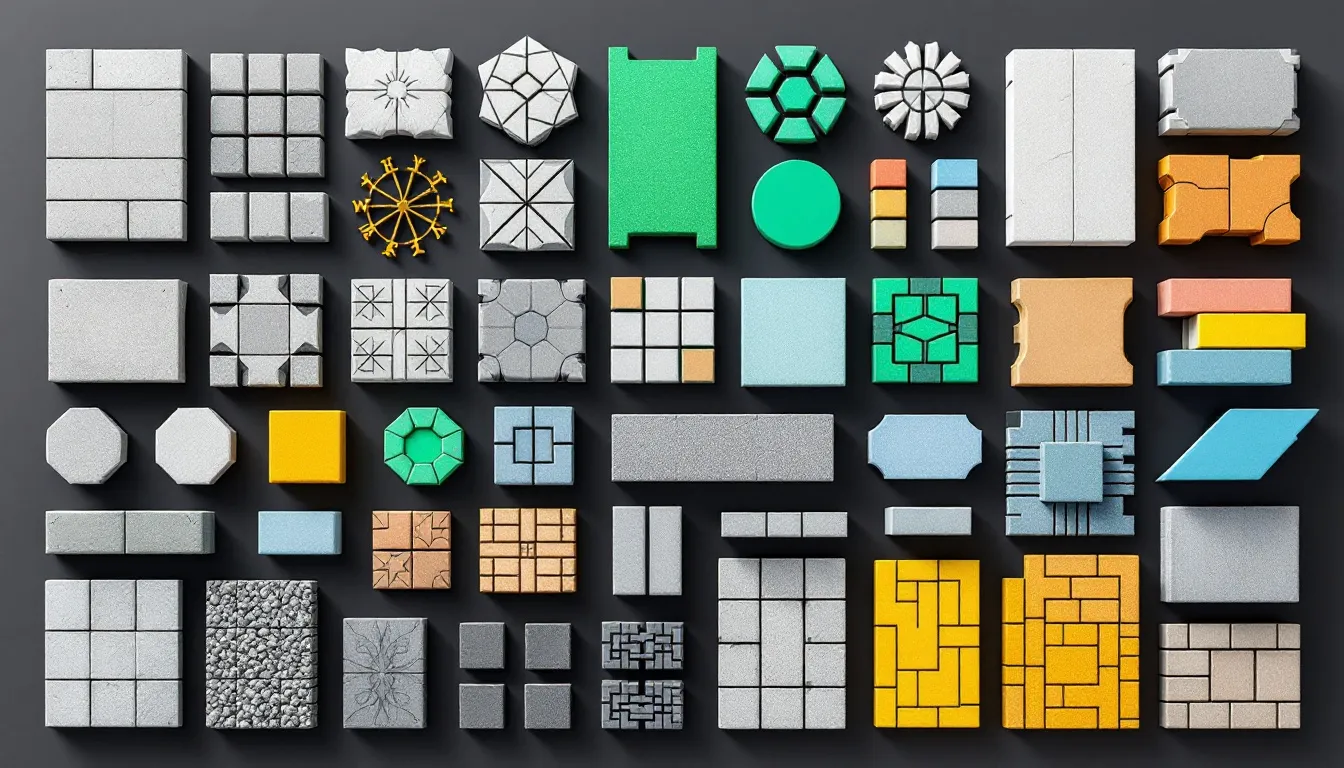
Paver blocks are solid, rectangular blocks made from concrete, designed for paving surfaces. They come in various shapes and sizes, including interlocking bricks, zig-zag, and square patterns, offering flexibility in design and application. Unlike traditional clay bricks, paver blocks are known for their strength, durability, and aesthetic appeal. They are commonly used in constructing footpaths, driveways, parks, and other outdoor spaces, providing a robust and visually pleasing paving material.
The manufacturing process of paver blocks involves mixing raw materials like cement, sand, and aggregates, pouring the mixture into molds, and then curing them to gain strength. The versatility of paver blocks makes them a preferred choice over conventional bricks and traditional clay bricks in many construction projects.
With the ability to withstand heavy loads and harsh weather conditions, paver blocks are an essential component in modern construction.
Why Start a Paver Block Making Business?
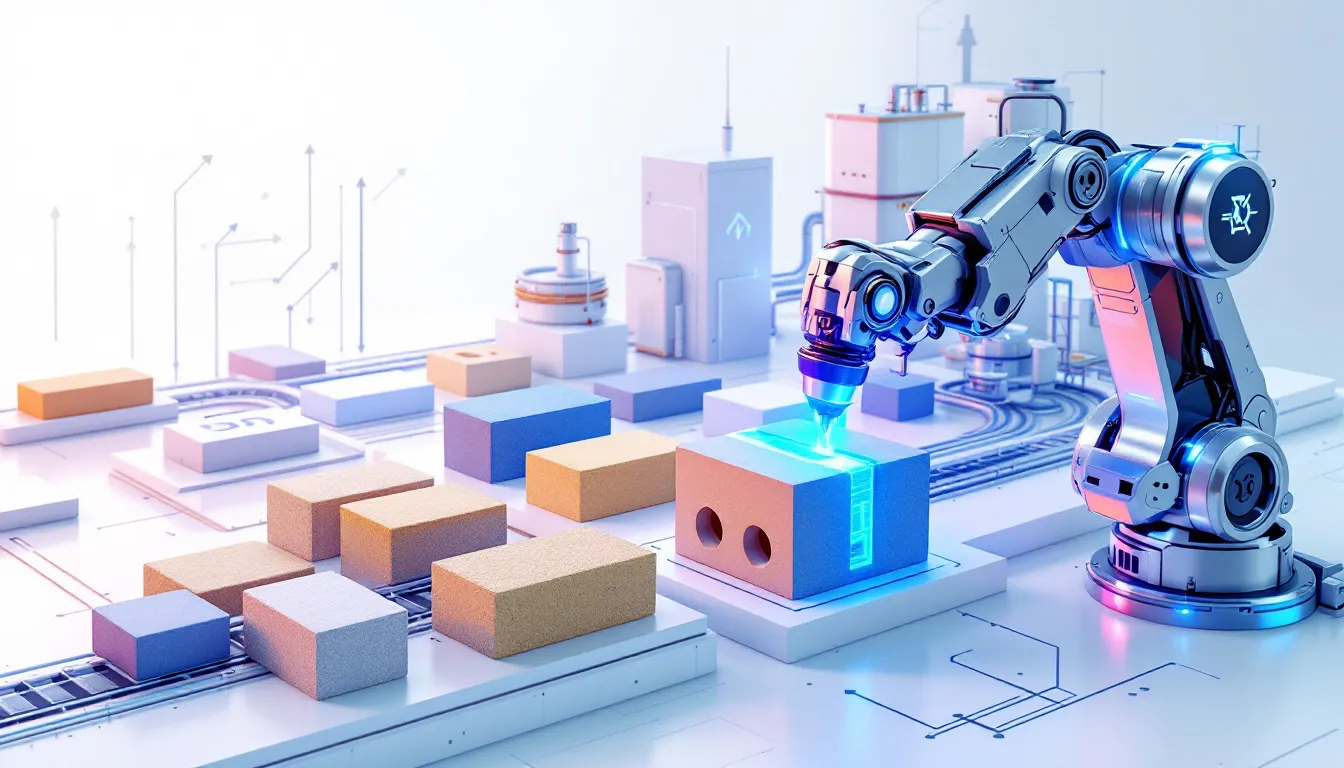
Starting a paver block making business offers several compelling advantages:
- Low Initial Investment: The initial investment required is relatively low compared to other manufacturing businesses, making it accessible for new entrepreneurs.
- Scalable Machinery Options: Machinery options range from manual to fully automatic, allowing entrepreneurs to start small and scale up as demand increases.
- High Market Demand: The market demand for paver blocks is high and continues to rise, driven by urbanization and the increasing focus on infrastructure development.
- Straightforward Manufacturing Process: The manufacturing process is straightforward, involving mixing, molding, and curing, which means that even those with minimal technical knowledge can operate a paver block manufacturing plant.
- Eco-Friendly Production: Paver block manufacturing is eco-friendly, as it can utilize waste materials like fly ash, reducing the environmental impact.
- Government Support for Infrastructure: With the government’s focus on infrastructure development, there are numerous opportunities for entrepreneurs to secure contracts for supplying paver blocks to various projects.
- Lucrative Business Opportunity: In summary, the paver block making business is a lucrative venture with low entry barriers, high market demand, and a straightforward manufacturing process, making it an attractive option for entrepreneurs looking to enter the building materials industry.
Market Potential in India
- Rapid Urbanization: India’s rapid urbanization fuels the demand for paver blocks in both residential and commercial spaces, making them a popular choice in modern construction.
- Booming Real Estate Sector: The real estate sector’s growth has significantly increased the use of paver blocks for various applications, including footpaths, driveways, and large-scale infrastructure projects.
- Government and Private Projects: Both sectors increasingly favor paver blocks due to their durability and aesthetic appeal, further boosting demand.
- Rural Adoption: Modern construction practices are being adopted in rural regions, expanding the market potential for paver blocks beyond urban areas.
- National and Export Potential: Strong local demand and considerable national and export potential, with Indian manufacturers supplying paver blocks to neighboring countries.
- Focus on Sustainable Materials: Rising awareness of sustainable building materials positions paver blocks as a preferred choice in construction projects.
- Infrastructure Development: India’s focus on infrastructure development presents extensive opportunities for the paver block industry to supply materials.
Setup Requirements
Setting up a paver block manufacturing plant involves several key requirements. Firstly, you will need a suitable piece of land or a shed to house the plant. The type of machinery required depends on your production capacity and budget, ranging from manual and semi-automatic to fully automatic machines.
Raw materials like cement, sand, aggregates, and water are essential for production, and understanding the costs raw material requirements is crucial. Additionally, a reliable workforce is crucial for efficient operations, and you will need a steady supply of electricity and water to keep the plant running smoothly.
Step-by-Step Guide to the Paver Block Manufacturing Process
- Material Preparation: Gather and measure the raw materials, including cement, sand, aggregates, and any additives required for the specific type of paver block being produced.
A thorough understanding of the unit operations involved in the manufacturing process is essential. This includes mass balance, raw material requirements, and quality assurance criteria.
- Mixing: Combine the raw materials in a concrete mixer to ensure a uniform mixture. This step is crucial for achieving the desired strength and consistency of the paver blocks.
- Molding: Pour the mixed material into molds of the desired shape and size. This step involves using molds that can vary from simple rectangular blocks to intricate interlocking designs.
- Vibration and Compaction: Subject the filled molds to vibration and compaction using specialized machinery. This process ensures that the mixture settles properly, removing air pockets and increasing the density of the blocks.
- Curing: Allow the molded blocks to cure for a specified period. Curing is essential for the blocks to gain the necessary strength and durability. This step may involve keeping the blocks in a controlled environment with adequate moisture.
- Demolding: Carefully remove the cured blocks from the molds. This step requires precision to avoid damaging the newly formed paver blocks.
- Quality Inspection: Perform a quality check to ensure that the blocks meet the required standards for dimensions, strength, and appearance.
- Packaging and Storage: Once the blocks pass quality inspection, package them appropriately for storage or transport. Proper packaging ensures that the blocks remain intact and undamaged during handling.
- Distribution: Finally, distribute the finished paver
Investment Required
The initial investment required for setting up a paver block manufacturing plant can vary depending on several factors. The cost of land or a shed is a significant expense. You will also need to invest in machinery, with costs ranging from manual machines to fully automated systems. Raw materials like cement, sand, and aggregates are ongoing expenses that need to be accounted for.
Labor and utilities, including electricity and water, are additional costs that contribute to the overall investment. Lastly, working capital is necessary to cover day-to-day operational expenses.
In summary, the total investment required encompasses land acquisition, machinery procurement, raw materials, labor, utilities, working capital, and costs project economics. Detailed financial planning and securing project funding are essential for a successful setup. Net present value (NPV) is a crucial financial metric used to assess capital investments, project funding, operating expenses, and to evaluate the profitability of the project, thereby aiding stakeholders in making informed decisions regarding their investments and operations.
Profit Margin and Return on Investment
Understanding the profit margin and return on investment (ROI) is crucial for any business. The cost per block in a paver block manufacturing plant includes expenses for raw materials, labor, and utilities. The selling price per block is typically higher, allowing for a healthy profit margin. For instance, if the cost per block is $0.50 and the selling price is $1.00, the profit per block would be $0.50. Monthly profit calculations can provide a clearer picture of the business’s profitability.
A breakeven analysis helps determine the point at which the business starts making a profit. By calculating the total fixed and variable costs and comparing them with the revenue generated from block sales, you can identify the breakeven point. This financial analysis is essential for understanding the viability and profitability of the paver block manufacturing business.
Licenses and Legal Formalities
Starting a paver block manufacturing business requires obtaining several licenses and registrations to operate legally. The first step is to register your business with the MSME/Udyam portal to avail various benefits and schemes. GST registration is mandatory for tax compliance and to avail input tax credit.
A local trade license is necessary to operate within your municipal limits. Depending on the location and scale of your plant, you may also need a pollution NOC (No Objection Certificate) to ensure environmental compliance.
Marketing and Sales Strategy
- Target Audience Identification: Focus on builders, contractors, and local government agencies as primary consumers of paver blocks.
- Online Presence: Leverage digital platforms like Indiamart, JustDial, and WhatsApp to expand reach and generate leads.
- Bulk Discounts: Offer attractive discounts for large orders from construction companies and infrastructure projects to encourage bulk purchasing.
- Tenders Participation: Engage in tenders for government and private projects to secure substantial contracts.
- Traditional and Digital Marketing Mix: Combine traditional marketing methods with digital strategies to effectively reach and engage your target audience.
- Networking and Partnerships: Build strong relationships with key stakeholders in the construction industry to enhance credibility and increase sales opportunities.
- Customer Feedback and Improvement: Regularly collect customer feedback to refine products and services, ensuring customer satisfaction and loyalty.
- Brand Building: Focus on building a strong brand presence through consistent messaging and quality assurance to differentiate from competitors.
By implementing these strategies, you can effectively enhance your marketing efforts and drive sales for your paver block manufacturing business.
How Our Project Report Can Help You
- Comprehensive Guidance: Our project report offers a detailed roadmap for setting up a paver block manufacturing business, covering market overview, operational requirements, and financial projections.
- Time-Saving Resource: By providing clear and structured information, the report saves you time and reduces confusion in planning and executing your business setup.
- Bank Loan Assistance: The report contains all necessary details required by financial institutions, making it an invaluable tool when applying for bank loans.
- Invaluable for Entrepreneurs and Startups: Whether you are a student, an entrepreneur, or a startup, the report serves as a crucial resource for successfully launching your paver block manufacturing plant.
- Strategic Planning Tool: It aids in strategic decision-making by offering insights into market trends, investment opportunities, and risk management strategies.
- Enhanced Business Understanding: Gain a thorough understanding of the business landscape, including industry trends, regulatory requirements, and technological advancements.
- Investment Attraction: Use the report to attract potential investors by showcasing a well-researched and viable business plan.
- Operational Efficiency: Improve operational efficiency by understanding the machinery, technology, and raw material
Paver Block Manufacturing Plant Project Report Overview
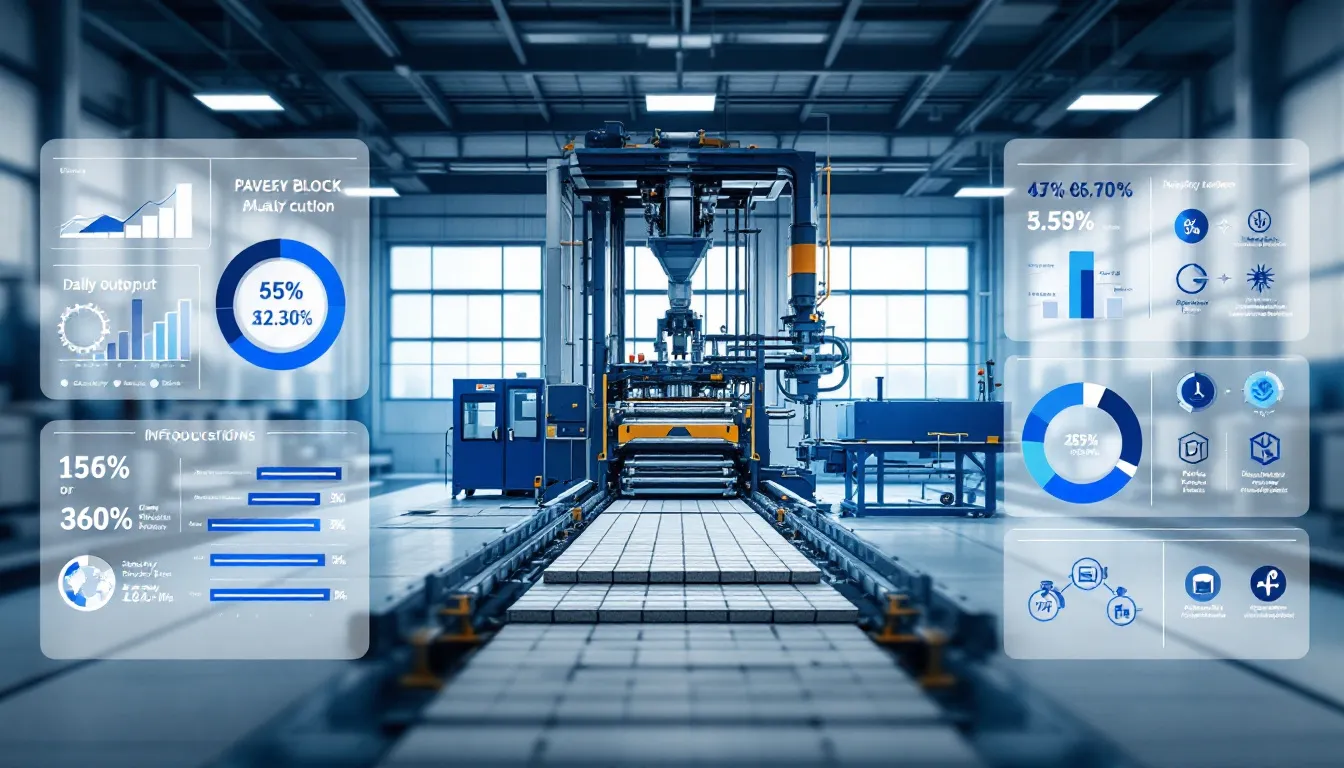
The project report for a paver block manufacturing plant outlines critical components such as market overview, operational requirements, and financial projections essential for establishing the business. This comprehensive market overview provides insights into industry trends, market potential, and the financial viability of the paver block manufacturing business.
Industry Trends and Market Analysis
- Urbanization and Construction Growth: The paver block market is experiencing significant growth due to rapid urbanization and increased construction activities worldwide.
- Government Initiatives: Various government initiatives aimed at infrastructure development are driving the demand for paver blocks, particularly interlocking types.
- Sustainable Construction Solutions: There is a rising demand for sustainable and durable construction materials, with paver blocks being a preferred choice for eco-friendly projects.
- Interlocking Paver Block Expansion: The market for interlocking paver blocks is projected to expand significantly, supported by advancements in manufacturing technologies.
- Soil Erosion and Water Drainage Solutions: Permeable paver blocks are gaining popularity for their ability to mitigate soil erosion and improve water drainage.
- Consumer Preferences: Increasing consumer preference for low-maintenance and visually appealing surfaces is boosting the demand for paver blocks.
- Revenue Forecasts: Market demand, pricing strategies, and production capacity are key factors influencing revenue projections in the paver block industry.
- Raw Material Price Fluctuations: Fluctuations in the prices of raw materials like cement and aggregates impact production costs and profitability.
- Competitive Landscape: Manufacturers face competition from alternative paving solutions, necessitating innovation and differentiation in the market.
- Risk Factors: Industry risks include fluctuating raw material prices and regulatory compliance challenges, which can affect market dynamics.
Product Overview and Types
Paver blocks come in various types, with interlocking paver blocks being notable for their unique design. These blocks feature edges that fit together like puzzle pieces, providing stability and customization for irregular shapes and sizes. Interlocking bricks, an improved version of traditional clay bricks, typically measure 230x100x75mm and cost between $0.5 to $2.
Interlocking bricks achieve stability through shear-key and lock mechanisms that allow them to interlock firmly. This interlocking nature significantly aids in distributing seismic forces equally during earthquakes, enhancing structural integrity.
This product overview unit operations provide a broad market overview of the types and features of paver blocks.
Plant Setup and Infrastructure Costs
Establishing a pavers block manufacturing plant involves multiple phases, including land acquisition, site development, and infrastructure investment.
This section will delve into the specifics of site selection and development, as well as construction costs.
Site Selection and Development
Proximity to raw materials and transportation infrastructure is critical when evaluating potential sites for a paver block manufacturing facility. Key factors in site selection include access to transportation, which facilitates the timely delivery of materials and distribution of products.
The availability of skilled labor is essential for efficient plant operations and should be considered when choosing a site. Selecting an appropriate site for the paver block manufacturing plant is crucial for its operational success. The development plant layout must accommodate these factors to ensure smooth operations.
Construction Costs
Construction costs for a paver block plant include expenditures on site preparation, building structures, and installing machinery. These costs can vary greatly depending on location, size, and design of the facility.
Detailed budgeting for construction must account for land acquisition, building materials, labor, and utility installations. The construction of paver blocks involves risks such as material quality fluctuations and supply chain disruptions, which can impact project timelines and costs. Understanding these direct and indirect costs is essential for accurate financial analysis and project economics.
Machinery and Technology Requirements
Setting up a paver block manufacturing facility involves several key components, including infrastructure, machinery, and raw materials. The production of interlocking paver blocks requires specialized machinery to enhance efficiency and precision.
Key Points on Machinery and Technology Requirements
- Hydraulic Pressure Machines: Essential for applying the necessary force to shape and compact the paver blocks, ensuring durability and strength.
- Block Making Machines: Available in manual, semi-automatic, and automatic variants, these machines are crucial for producing consistent and high-quality paver blocks.
- Concrete Mixers: Used to achieve a uniform mixture of raw materials, which is vital for the structural integrity of the paver blocks.
- Hydraulic Presses: Enhance the compaction process, producing denser and more resilient blocks.
- Curing Chambers: Provide a controlled environment for curing paver blocks, ensuring they gain the required strength and durability.
- Automation and Modern Vibration Technology: Recent advancements include automated batching systems and modern vibration technology, which improve mixing consistency and compaction.
- Energy-Efficient Machinery: Implementing machinery with energy-saving features can reduce electricity costs by up to 30%, contributing to lower operational expenses.
- Production Capacity: Machines can produce between 1,000 to 1,500 blocks per hour, depending on the model and automation level.
- Innovations in Design: Newer machines offer features like hydraulic stands for easier operation and improved designs for a smoother finish on paver surfaces.
- Technological Advancements: The integration of advanced technologies in machinery enhances production efficiency and allows for the creation of multi-colored tiles.
Choosing the right machinery is essential for optimizing production efficiency and ensuring high-quality output of paver blocks. These technological developments are crucial for staying competitive in the industry.
Raw Material Requirements and Costs
- Key Materials: Essential raw materials for manufacturing paver blocks include crushed stone dust, stone aggregate, and Ordinary Portland Cement (OPC). These materials form the core components of concrete paving blocks, known for their durability and aesthetic appeal.
- Additional Components: Water and optional additives are also required to enhance the quality and performance of the paver blocks. These additives can improve properties like strength, color, or setting time.
- Ongoing Costs: The production process involves ongoing costs, such as raw materials, labor, utilities, and maintenance expenses, which are crucial for maintaining consistent production quality.
- Supplier Relationships: Building strong relationships with reliable suppliers is vital for mitigating risks related to material shortages and price fluctuations. This ensures a steady supply of high-quality raw materials.
- Price Trends: Fluctuations in raw material prices can significantly impact production costs. Monitoring market trends and price trends is essential for effective financial planning and maintaining profitability.
- Concrete Blocks Advantage: Concrete blocks, including interlocking bricks, are favored for their low maintenance and ability to withstand various weather conditions, making them a preferred choice in both residential and commercial spaces.
- Cost Management: Diversifying suppliers and maintaining a buffer stock of raw materials can help manage costs and reduce the impact of price volatility on production expenses.
- Impact on Final Product: The quality of raw materials significantly affects the durability and appearance of concrete paving blocks. Consistent material quality ensures that the final product meets strength and aesthetic standards, making strict quality control essential.
Human Resource and Utility Requirements
Efficient operation of a paver block manufacturing plant requires careful consideration of workforce and utility needs. Here are the key points to consider:
Workforce Requirements
- Diverse Skill Set: A skilled workforce is essential, including expertise in machinery operation, quality control, and maintenance.
- Number of Employees: The number of employees needed varies based on production capacity and operational complexity.
- Training Programs: Investing in training can enhance skill sets and improve productivity and product quality.
- Labor Costs: Labor costs are a significant part of overall expenses and must be carefully managed to maintain profitability.
Utility Requirements
- Electricity: A reliable electricity supply is crucial for operating machinery and ensuring uninterrupted production.
- Water Supply: Adequate water supply is necessary for mixing materials and curing paver blocks.
- Waste Management: Efficient waste management systems must be in place to handle byproducts and maintain environmental compliance.
- Cost Estimation: Accurate estimation of utility costs is essential for financial planning and budgeting.
These requirements are critical for maintaining efficient operations and ensuring the success of a paver block manufacturing plant.
Financial Analysis and Project Economics
Establishing a paver block manufacturing plant involves analyzing project funding, equipment costs, and operational expenses. A comprehensive financial analysis for a paver block manufacturing project includes capital investments, operating costs, and revenue forecasts.
A thorough financial assessment encompasses the evaluation of both capital and operational expenditures, aiming to determine potential profitability and return on investment. This section will delve into the specifics of capital investments, operating expenses, and revenue projections.
Capital Investments
Setting up a paver block manufacturing plant requires significant initial capital outlay, which includes expenses for land acquisition, machinery, and plant infrastructure. Setting up a paver block manufacturing plant generally requires an initial investment ranging from rupees 20 Lakhs to 50 Lakhs, primarily for machinery and technology.
The capital investments in a paver block manufacturing setup typically encompass expenses related to land, machinery, and initial setup processes. Initial investment for establishing a paver block plant includes land acquisition, construction costs, and machinery procurement.
Initial capital outlays for setting up a paver block manufacturing plant include machinery, land, and construction costs.
Operating Expenses
The cost of raw materials for paver blocks has shown fluctuations, significantly influenced by changes in market demand and production efficiency. Hiring skilled labor can improve production efficiency, with industry reports suggesting that up to 40% of production efficiency is linked to skilled workers.
Ongoing training programs for employees can enhance their skills and improve overall product quality in the manufacturing process. Operating expenses in a paver block manufacturing plant encompass ongoing costs necessary to maintain production and quality standards.
Revenue and Profit Projections
The block paving industry is projected to grow from approximately USD 5.5 billion in 2024 to about USD 7.55 billion by 2032, reflecting a compound annual growth rate of 4.00% during this period. The global market for interlocking paver blocks is projected to grow from USD 4.5 billion in 2024 to USD 7.2 billion by 2033, indicating a robust increase driven by urbanization and sustainability trends.
These projections provide a clear picture of the industry’s growth potential and the revenue opportunities for businesses in the paver block manufacturing sector. Understanding these financial metrics is crucial for making informed investment decisions and ensuring long-term profitability.
Regulatory Procedures and Certifications
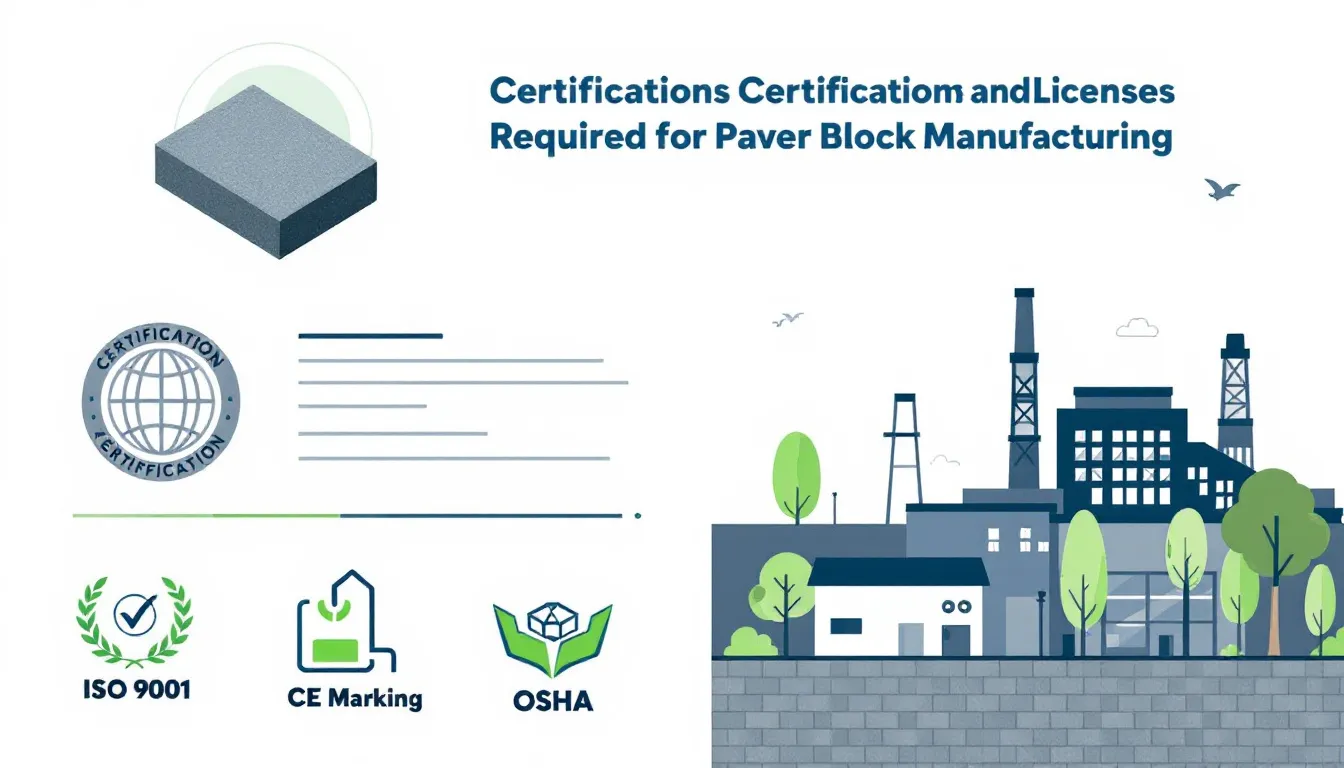
Compliance with local and national regulations ensures the paver block manufacturing plant operates legally and adheres to safety and environmental standards. The compliance requirements for a paver block manufacturing plant often include obtaining the necessary business licenses, environmental clearances, and adherence to labor laws.
This section will detail the compliance requirements and key certifications needed for a paver block manufacturing plant.
Compliance Requirements
The environmental impact of the chosen site must be assessed to ensure compliance with local regulations and sustainable practices. Environmental impact assessments are crucial in evaluating potential sites for a paver block manufacturing plant.
To meet compliance, manufacturers must secure BIS certification, which involves rigorous testing of paver blocks for durability and strength. Manufacturers must establish a compliant testing facility that meets BIS standards to ensure consistent quality control of paver blocks.
Regulatory compliance can present challenges, as manufacturers must adhere to local standards that can vary significantly. Compliance is crucial in the paver block manufacturing process to ensure quality and adherence to regulations.
Key Certifications
The ISI Mark is essential for paver blocks, signifying they meet the quality benchmarks set by BIS under the IS 15658:2021 standard. The ISI Mark ensures that the products adhere to established safety and quality standards, which is crucial for market acceptance.
Key documentation necessary for BIS certification includes product specifications, manufacturing process details, and raw material test certificates. Obtaining these key certifications is essential for maintaining product quality and gaining market trust.
Packaging, Transportation, and Logistics
Packaging plays a crucial role in protecting paver blocks during transport and storage. Packaging materials and methods used for paver blocks include sturdy containers or pallets designed to prevent damage.
Transportation logistics for paver blocks must consider factors such as weight, volume, and delivery timelines. Transportation costs for delivering paver blocks can vary based on distance, mode of transportation, and fuel prices.
Packaging Requirements
Common packaging materials for paver blocks include shrink wrap, cardboard boxes, and wooden pallets. These packaging materials provide stability and protection, preventing damage during handling and transport.
Packaging plays a crucial role in ensuring the safety and integrity of paver blocks during distribution.
Transportation Costs
Transportation costs are crucial for the profitability of delivering paver blocks to various markets, requiring detailed analysis and planning. Key transportation costs include fuel expenses, vehicle maintenance, and labor costs for delivery personnel.
Efficient logistics must consider optimal packaging methods to minimize damage during packaging and transportation requirements and reduce costs. Minimizing transportation and logistical costs can significantly enhance the overall profitability of the paver block manufacturing business.
Risk Factors and Management Strategies
The paver block manufacturing industry faces several critical challenges that can impact business operations and profitability. Here are the key risk factors and corresponding management strategies:
Risk Factors
- Fluctuating Raw Material Prices: Variations in the cost of cement, aggregates, and other materials can affect production costs and profit margins.
- Supply Chain Disruptions: Delays or shortages in raw material supply can halt production and lead to financial losses.
- Regulatory Compliance Issues: Navigating complex regulations and obtaining necessary certifications can be challenging, impacting operational legality.
- Market Demand Variability: Changes in construction trends and economic conditions can affect the demand for paver blocks.
- Technological Advancements: Keeping up with rapid technological changes is necessary to maintain competitiveness.
- Competition: Intense competition from alternative paving solutions and other manufacturers can pressure pricing and market share.
Management Strategies
- Diversifying Suppliers: Establish relationships with multiple suppliers to mitigate the risk of raw material shortages and price fluctuations.
- Implementing Quality Control Systems: Regularly monitor production processes to maintain consistent quality and meet regulatory standards.
- Investing in Technology: Upgrade machinery and adopt new technologies to enhance production efficiency and product quality.
- Market Research and Adaptation: Continuously analyze market trends and adjust product offerings to meet changing consumer preferences.
- Cost Management: Implement cost-saving measures and optimize operational efficiency to maintain profitability.
- Building Strong Brand Presence: Focus on brand building and customer loyalty to differentiate from competitors and secure a stable market position.
By addressing these risk factors with effective management strategies, businesses can ensure sustainable growth and success in the paver block manufacturing industry.
Investment Opportunities and Market Forecasts
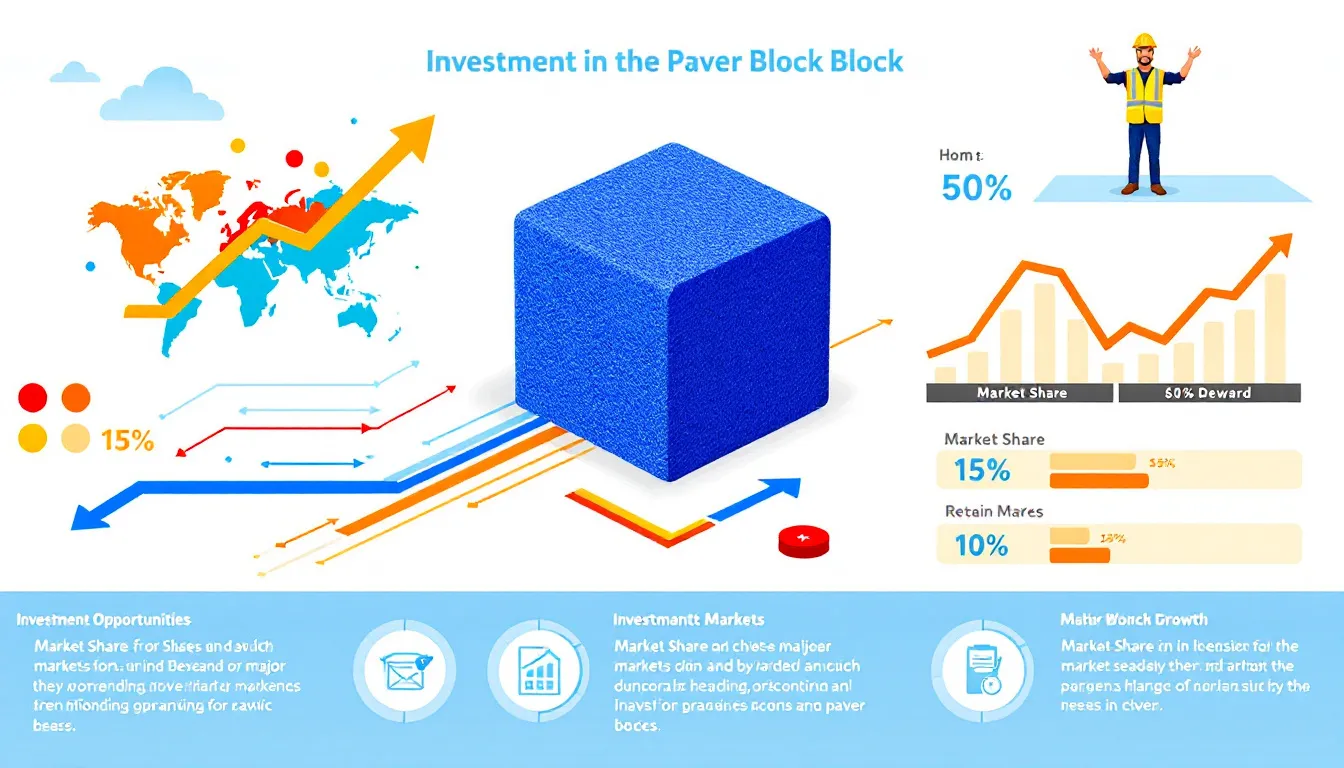
- Rising Demand: Urbanization and the preference for sustainable construction materials are driving the demand for paver blocks.
- Infrastructure Development: Regions experiencing infrastructure growth present lucrative investment prospects in paver block manufacturing.
- Sustainable Solutions: The eco-friendly nature of interlocking paver blocks, such as their water permeability, enhances their appeal.
- Machinery Innovations: Advancements in machinery that improve production efficiency and quality encourage sector investment.
- Aesthetic Landscaping: Increased demand for visually appealing and sustainable landscaping solutions opens new investment avenues.
- Comprehensive Market Insights: A broad and comprehensive market overview highlights the profitability potential in this industry.
Market Forecasts
- Growth Projections: The paver block machine market is expected to reach approximately $2.1 billion by 2030, with a CAGR of 7.8% from 2024 to 2030.
- Interlocking Paver Expansion: The interlocking paver block market is anticipated to grow at a CAGR of 6.5% between 2026 and 2033.
- Emerging Markets: Asia-Pacific and Africa are poised for significant growth due to ongoing infrastructure projects.
- Technological Advancements: Innovations in manufacturing are diversifying paver block designs, boosting market prospects.
- Transportation Costs: Varied transportation expenses based on distance and regional factors influence overall market dynamics.
- Investor Insights: These forecasts provide a comprehensive market overview, aiding investors in making informed decisions.
Summary
In conclusion, the paver block manufacturing industry presents a promising investment opportunity with its growing market demand, low initial investment, and high profitability. The comprehensive market overview and industry trends indicate a robust growth trajectory driven by urbanization and the increasing focus on sustainable construction solutions. Setting up a paver block manufacturing plant requires careful planning, including understanding the setup requirements, financial analysis, and regulatory compliance.
By leveraging the information provided in this blog post, entrepreneurs and investors can make informed decisions and successfully navigate the challenges of the paver block manufacturing business. With the right strategies and a clear understanding of the market, there is significant potential for growth and profitability in this industry.
Frequently Asked Questions
What are the initial investment requirements for setting up a paver block manufacturing plant?
The initial investment for establishing a paver block manufacturing plant generally falls between 20 Lakhs and 50 Lakhs. This amount covers expenses such as land acquisition, machinery, and necessary infrastructure.
What licenses and registrations are needed to start a paver block manufacturing business?
To start a paver block manufacturing business, you will need MSME/Udyam registration, GST registration, a local trade license, and potentially a pollution NOC based on your location and operational scale. These licenses and registrations are essential for legal compliance and smooth operation of your business.
What are the key raw materials required for manufacturing paver blocks?
The key raw materials required for manufacturing paver blocks are crushed stone dust, stone aggregate, ordinary Portland cement (OPC), water, and optional additives. Ensuring a proper mix of these materials is crucial for achieving high-quality paver blocks.
How can I market and sell my paver blocks effectively?
To market and sell your paver blocks effectively, target builders, contractors, and local government agencies while leveraging online platforms such as Indiamart and JustDial. Additionally, consider offering bulk discounts and participating in tenders to enhance sales opportunities.
What are the main challenges in the paver block manufacturing industry?
The main challenges in the paver block manufacturing industry include maintaining consistent quality due to fluctuating raw material availability, ensuring the stability of paver structures, and effectively addressing water drainage issues.